It’s no secret that to make a product well, you have to have a good team of people, quality materials, and the right tools for the job. Plus, it never hurts if you know what you’re doing. Fenetex products are custom made in the USA using imported parts based on the specifications supplied through an online portal. We like to think of what we do as mass customization, and it is incredibly challenging to do it right. To be able to do it well, you need to have the resources to be able to invest in your business.
Since we started making screens, we have used automation to help our production team make a more accurate product faster. A digital revolution is underway in manufacturing and Fenetex is spending millions of dollars on equipment, production lines, and software to be as efficient and accurate as possible.
Common Features
Common features are features shared by all the screens Fenetex manufactures. All of these components are designed by Fenetex and manufactured by trusted partners with whom we have long standing relationships. The inherent quality of the parts we design is one of the reasons we can offer a lifetime warranty.
Fenetex hoods and reels seamlessly match any side track and screen type. Our system automatically selects the appropriate hood and reel based on your order’s dimensions and screen type. We exclusively utilize extruded aluminum hoods and reels, recognized as the superior materials for strength and corrosion resistance.
Our Welding Process
Fenetex keder is an assembly where a PVC cord is overwrapped by a low-friction PVC-coated fabric that can be attached to a screen edge.
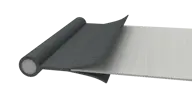
One
Perfecting Keder Performance over a Decade
We've engineered our keder with specific cord hardness, fabric densities, and PVC coatings. Our formula for this has been perfected over a decade of manufacturing and real-world use to ensure the best possible performance.
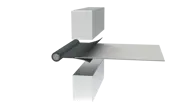
Two
A High-Energy Joining Process
A precisely cut screen edge is inserted into a Fenetex keder. Welding bars located above and below the screen will come together when the welding cycle is initiated.
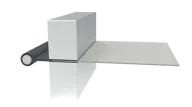
Three
The Molecular Level Fusion of Keder and Screen
When the welding cycle is initiated, the bars clamp down on the materials with a precise amount of pressure. Then, 10kW of RF energy is briefly pulsed through the material. This creates a lot of heat, welding the materials together. Finally, a cooling phase under pressure sets the weld.
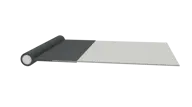
Four
Backed by a Lifetime Warranty
Once the weld cycle is complete, the keder and the screen are now permanently joined at the molecular level and cannot be separated. There are no zippers to break, no adhesives to fail, and no stitching to wear out. Our process is so reliable that our screens are backed by a lifetime warranty.